The central feeding system is designed for the production of plastic products in the injection workshop, enabling uninterrupted unmanned continuous molding operations. The variety of raw materials and the combined use of multi-color materials can be changed as needed to automate the coloring process. The system can regenerate and use the cold injection material in a fully automatic way, can control all the feeding equipment, and prevent the occurrence of blockages in the storage bin. It is fully automated by setting a central monitoring station.
system introductionThe central centralized feeding system adopts microcomputer centralized automatic control, which realizes 24-hour continuous feeding operation for pellets. Multiple small microcomputers separately control the coloring process of each molding machine, with accurate measurement and uniform mixing, and can flexibly change the color to meet the requirements of multiple colors and varieties of products. According to the production volume of different molding machines, the feed volume can be flexibly changed. The design of multiple feed pipes can ensure the diversified requirements of the main materials. The system has multiple monitoring and protection functions, and the work is safe and reliable. The aliases of the central feeding system are: centralized feeding system, automatic feeding system, etc.
Central feeding system working principleThe central feeding system adopts vacuum conveying method, and the plastic raw materials are transferred from the storage tank to the central dehumidification and drying system through a centralized pipeline system, and then the dried raw materials are transferred to each injection molding machine. The central feeding system adopts the design method of "one machine and one pipe" to ensure that the air of the entire system conveys the raw materials to prevent the moisture from drying and drying. At the same time, the operation of each transmission is stable, and no blocking phenomenon occurs. It is used in conjunction with the central dehumidification and drying system, which can be used to clean the pipeline after the dehumidification, drying and circulation, to ensure that there is no residual particulate material in the pipeline. Consistent. Under the vacuum negative pressure, the dust in the raw materials will be filtered through the dust filtration system, which helps to improve the quality of the molded products.
Central feeding system compositionCentral console, cyclone dust collector, high-efficiency filter, fan, branch station, drying hopper, dehumidifier, material selection rack, micro-moving hopper, electric eye hopper, air cut valve, material cut valve.
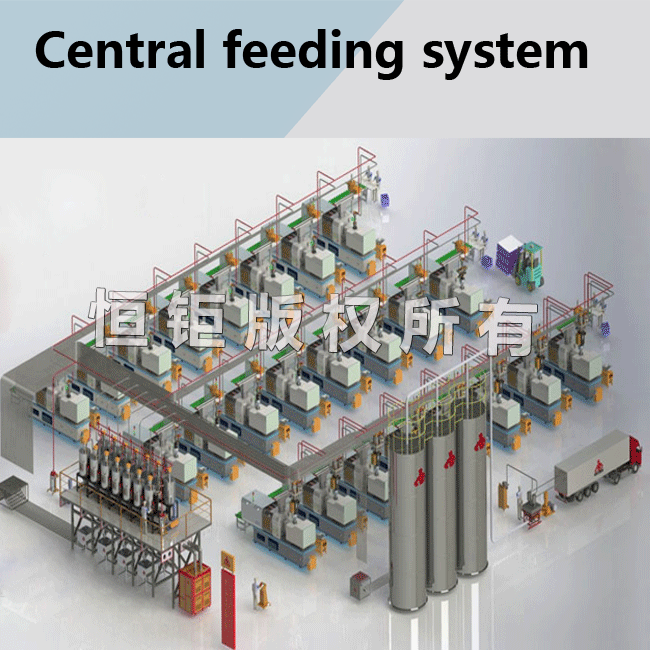
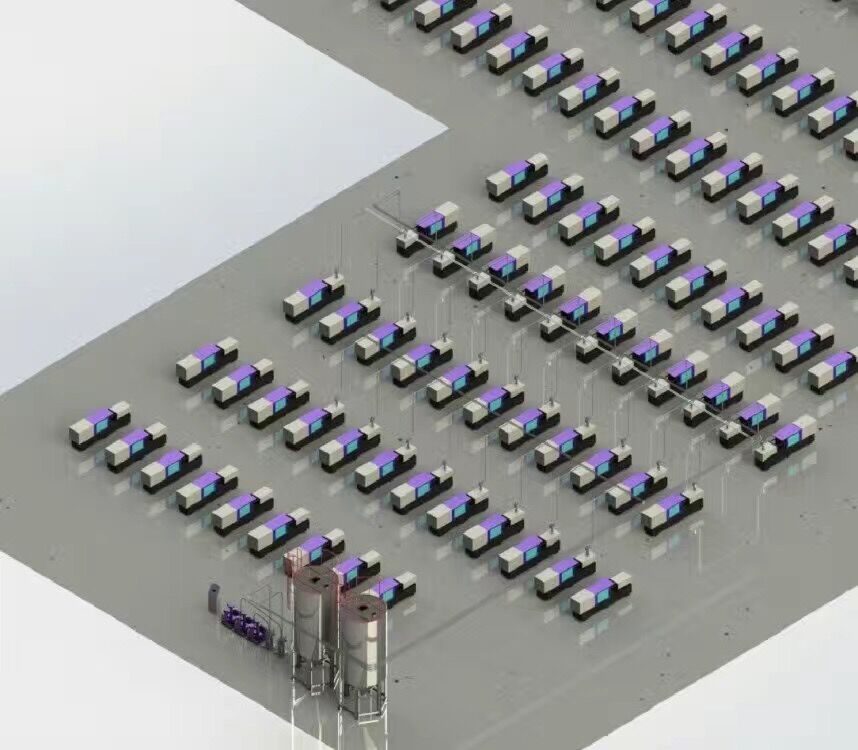
Features1. Efficient: The central feeding system can realize the automatic supply of various raw materials to any injection molding processing equipment in multiple chambers, which can include the drying processing of raw materials, color matching processing, and the utilization of proportionally crushed recycled materials. Automation control, monitoring, etc., and can meet the 24-hour non-stop production needs. Second, energy saving: the central feeding system is easy to operate, and only a few people can control the feeding requirements of the entire injection molding plant, thereby reducing a lot of labor costs. Secondly, the raw material belt and corresponding auxiliary equipment beside the injection molding machine are reduced, and the space utilization rate is improved. In addition, due to the use of the central feeding method, correspondingly reducing a lot of stand-alone equipment, it also saves electricity and reduces maintenance costs. 3. Personalization: The central feeding system can achieve different users, different workshop characteristics, and different requirements for the use of raw materials. Can be designed according to actual needs to optimize the program. Fourth, the image of a modern factory: the central feeding system will minimize the pollution of raw materials and dust on injection molding production, so that it can maintain a clean production workshop. The environmental protection effect is to reach the standard of 100,000 clean room operation requirements, and reduce the noise, and finally can realize the unmanned automated production workshop, and establish the image of modern factory management.
Central feeding system Design FlowRaw materials → storage → metering → drying → conveying → use The central feeding system adopts one machine and one tube, and the sealed circuit design method ensures the stable operation of the entire system, and there is no phenomenon of plastic moisture regain and blockage. It is used in conjunction with a central dryer (dehumidifier) system to allow the dry air to dry the raw materials again to prevent the plastic from regaining moisture after drying. At the same time, the conveying pipe is cleaned after each conveying cycle to ensure that there is no residue in the pipeline. While avoiding the resurgence of raw materials, it also ensures the consistency of the raw materials added to the injection molding machine. Under the action of the vacuum and negative pressure, the original dust in the raw materials is filtered out through the filter (dust collector) system, which is beneficial to improve the quality of the product.
Central feeding system Built-in introductionFeatures of the center console: 1. Adopt PLC and large-size 10.4-inch color man-machine interface touch panel, easy to understand and easy to operate; 2. Color-coded written display of various settings, operation and operation status; 3. Equipped with material tube evacuation and cleaning pipe, automatic dust washing and dust collection central feeding host A, B alternate automatic switching and manual material selection error prevention function; 4. A raw material control screen is added to monitor the raw materials used by each molding machine, suction materials, lack of materials and various abnormal phenomena of the central host (motor). Features of Puda Central Feeding Host: 1. The design of the motor does not stop to avoid frequent start of the motor and cause wear and tear; 2. With a safety pressure relief valve, when the main unit's motion pressure is too large, the safety setting value is overloaded, and the pressure relief valve automatically releases pressure to protect the motor; 3. The two A and B of the feeding host are alternated, and there is an automatic switching valve design to ensure the stability of raw material delivery. Features of automatic reversal cyclone dust collector: 1. Integrated design of air filter and cyclone dust collector to collect dust efficiently with natural centrifugal force; 2. It can be attached with a high-pressure gas tank and automatically clean the filter; 3. The dust collector is equipped with an air cut valve, which can effectively move the dust of the dust collector without stopping the machine. Features of fast feed station (Fenqi station): The branching station is composed of several branches, and the raw material of the same branching pipe can be used for the injection molding machine. Each branch has a quick press-to-head airtightness; it can improve the system efficiency and facilitate quick and easy material changes.
How to use the central feeding system, centralized feeding system and automatic feeding system accurately and safely? First of all, make sure that the feeder of the central centralized feeding system is stable and firm, whether there is loose or skew phenomenon, and do the cleaning work of the feeder's machine, so that it can not only improve its use efficiency, but also extend its service life.
1. Implement a system of dedicated personnel management responsibility and stand-alone operation responsibility for the central centralized feeding system. A maintenance file shall be established for the maintenance of the central centralized feeding system, and daily operation and maintenance records shall be recorded.
2. After cleaning the suction hopper and drying barrel, they should be installed in place, and the filter of the central centralized feeding system should be cleaned on time.
3. Protect the motor of the central centralized feeding system in time. If it is found that the motor does not turn or stops, check and repair it in time.
4. Regularly maintain and maintain the single machine in the central centralized feeding system, and regularly check the transmission pipeline, especially the vacuum pipeline and compressed air line for leaks.
5. Regularly use lubricating oil for the production and maintenance of the feeder of the central centralized feeding system. Make regular inspections of the power cord every day to see if the power cord is exposed. If there is a timely replacement of the power cord.
Guide to maintenance and update of central feeding systemIn order to obtain qualified plastic products and ensure the safety of people and equipment, the central feed system management system is specially formulated as shown below. 1. Through the establishment and implementation of the central feeding system management system, adhere to the daily maintenance of the central feeding system, ensure the normal use of the central feeding system, eliminate hidden dangers of accidents, improve work quality and production efficiency, and ensure smooth production.
(1) Regulations for the safe operation of the central feeding system 1. It is not allowed to make operation methods that may cause personal injury or damage the central feeding system for any reason or excuse. Personnel who have not received training in operation skills and who do not understand the structural principles and performance of the central feeding system (that is, technicians who are not designated by the company) may not adjust the machine. 2. In the case where the hopper of the central feeding system does not discharge, it is forbidden to use metal rods and rods, and poke the hopper roughly to avoid damage to the material. If the split screen, screen cover and magnet holder in the bucket are in the rotating state of the screw, it is very easy for the metal rod to be caught in the barrel and cause serious damage to the equipment. 3. It is strictly forbidden to start the central feeding system under load. After the central feeding system is started, it must be idle for 1 minute before it can be put into normal operation. 4. Before starting the central feeding system, preheat the plasticizing temperature to the set value and wait 3 to 5 minutes before driving the screw to melt the glue. It is strictly forbidden to touch the heating part with hands and other body parts. 5. No objects are allowed to be stacked in front of each electrical box and fire hydrant door to ensure that all evacuation channels are unobstructed. 6. No one should suddenly cut off the power supply of the normally operating machine (except for special reasons), otherwise it will damage the machine. 7. During operation, you can only lock the mold first and then enter the shooting platform. 8. When you go to work, you should check whether the central feeding system is operating normally, whether the process parameters are appropriate, whether the mold is firmly fixed on the central feeding system, the cooling device (mold cooling, blanking port cooling, action oil cooling) and the lubrication device are normal . 9. Do not climb onto the top of the machine or reach into the safety door when the machine is moving. 10. When the machine is shut down, the rubber material in the melted rubber cylinder should be shot clean, no excess material should be left, and it is forbidden to turn off the electric heating and power switch when the machine is under stress. 11. All the power supply of the central feeding system must be reliably grounded and connected to zero. The wire terminals, rod seats, etc. should be connected in a standardized manner and the insulation is reliable. 12. Be sure to follow proper mold clamping procedures when the machine is in motion. Especially the low voltage protection device must be adjusted to be absolutely reliable. 13. When cleaning the melt barrel, ensure the phase melting of the material and prevent the material from overheating and decomposition, and the "Refilling Operation Rules" should be strictly observed. 14. Strictly abide by "Mold Change Operation Rules" when changing molds. 15. During the crushing operation, the crushed products must be crushed one by one. It is strictly forbidden to pour the whole box (bag) into the crushing at one time, so as to avoid overloading the crusher or mixing foreign objects to damage the blade. 16. In the case where the hopper does not discharge, it is not allowed to use metal rods and rods, and poke the hopper roughly to avoid damage to the material. If the split screen, screen cover and magnet holder in the bucket are in the rotating state of the screw, it is very easy for the metal rod to be caught in the barrel and cause serious damage to the equipment. 17. Before starting the machine, make sure that all safety devices are effective (safety lever position, safety stop, safety door limit switch, safety pulley and emergency stop switch). If there is any abnormality, it must be reported to the superior immediately for handling. Those who have not checked or risked starting before starting the machine shall bear all safety responsibilities and the management personnel shall take joint sanctions.
(2) Inspection and adjustment work items during the operation of the central feeding system The safety protection devices on the equipment (such as mechanical lock levers, stop plates, various safety protection switches, etc.) are not allowed to move casually, nor are they allowed to be modified or intentionally rendered useless. 1. Clean the machine tool, workbench and ground debris, oil stains and dust, and keep the workplace clean and tidy. 2. Lubrication system: check the lubrication condition of each friction part (lubricating grease and oil injection machine). 3. Hydraulic actuation system: the oil quantity and temperature of the actuating oil (35 ~ 65 ℃), abnormal inspection of the sound condition of the hydraulic pump, and inspection of the solenoid valves and cylinder oil pipes. 4. Electric heating system: temperature setting and actual value, heating condition of electric heater, temperature control ON / OFF action, whether the nozzle thermostat is normal. 5. Security check: ①Whether the clamping action stops when the safety door is opened. ②Check whether the emergency stop button is malfunctioning. ③ The maximum value of the system pressure shall not exceed the specified value of 140kg / cm2. ④ The low-pressure protection action focuses on the low-pressure starting point position and mold-locking confirmation position for inspection and adjustment. 6. Injection structure action: Confirm the action of the injection melt, confirm the injection pressure, flow, position, time and screw rotation, adjust whether there is debris piled under the material tube, and tighten the screw clamp block to check. 7. Cooling system: Check the cooling water pipe device, pass the cooling water to confirm whether there is water leakage, and whether the oil cooler pipe is smooth. 8. Refrigeration system: Check the set value of chilled water temperature and the actual cooling effect. 9. Electrical system: ①Check the working environment of the electrical box such as temperature, humidity, dustproof, etc. ②Check the operation status of exhaust fan. ③Check the running status of the motor. ④ Check the setting of each limit switch, transfer switch and each timer. ⑤Check the operation panel and parameter settings. 10. Unlock the mold structure, whether the hinge action of the machine is smooth, smooth, and without abnormal noise, whether the dynamic fixed template is balanced, and whether the forces of the four tie rods are even. 11. Ejection structure: check the ejection times and stroke control. 12. Semi-automatic and fully automatic, pay special attention to the shedding status of the manufactured products, and check whether the movement is smooth and smooth. 13. The safety protection devices (such as mechanical lock levers, stop plates, and various safety protection switches, etc.) on the equipment are not allowed to move casually, nor are they allowed to be modified or intentionally rendered useless.
|