There are many types of mechanical equipment used for drying operations in plastic processing and production. Plastic dryers can be divided into normal pressure and reduced pressure according to operating pressure (decompression dryers are also called vacuum dryers). According to the operation method, it can be divided into batch type and continuous type. According to the drying medium, it can be divided into air, plastic dryer flue gas or other drying media. According to the movement (material movement and drying medium flow), it can be divided into cocurrent, countercurrent and crossflow. The plastic dehumidification dryer keeps the compressed air pressure basically unchanged, lowering the temperature of the compressed air can reduce the water vapor content in the compressed air, and the excess water vapor will condense into liquid. Plastic dryers use this principle to dry compressed air using refrigeration technology.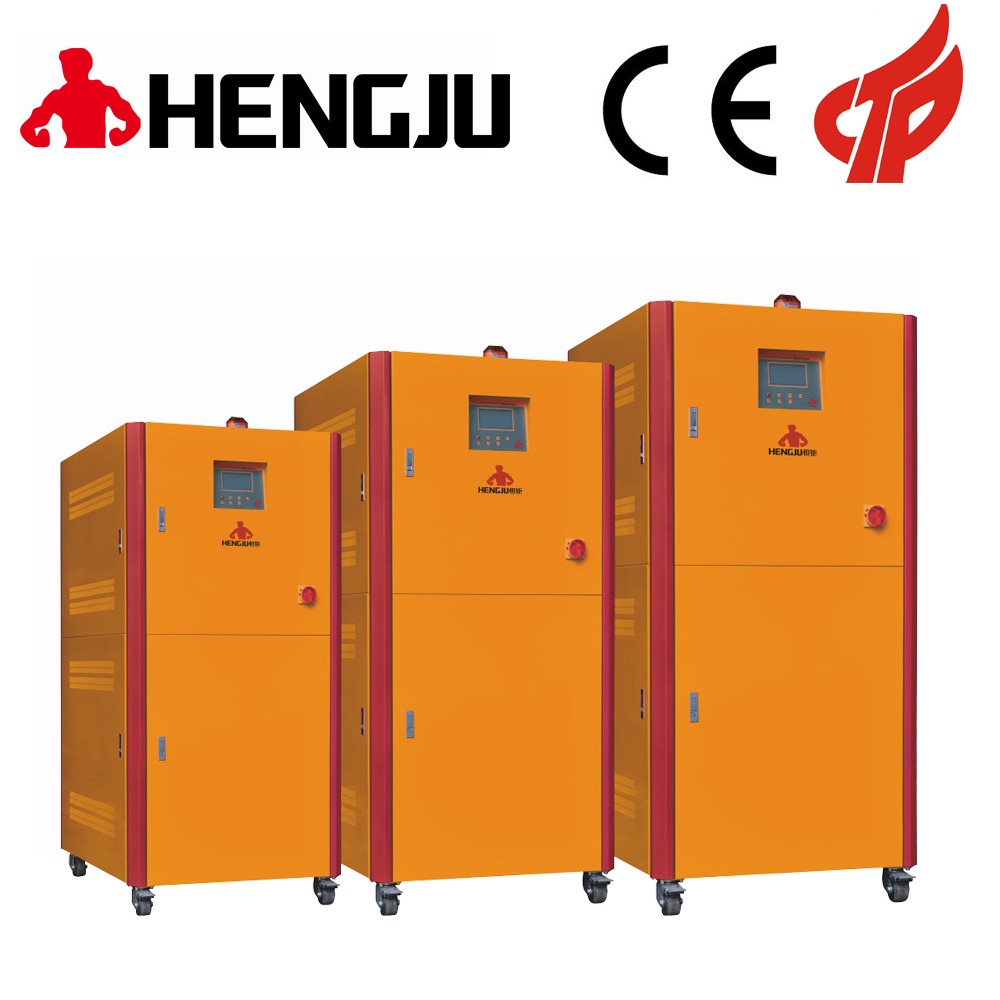
The refrigeration system of the plastic dryer freeze dryer is a compression refrigeration, which is composed of four basic components such as a refrigeration compressor, a condenser, an evaporator, and an expansion valve. They are connected in sequence with pipes to form a closed system. The refrigerant circulates continuously in the system. The plastic dryer changes state and exchanges heat with compressed air and cooling medium. Compressed air dryers also have adsorption dryers and dissolution dryers.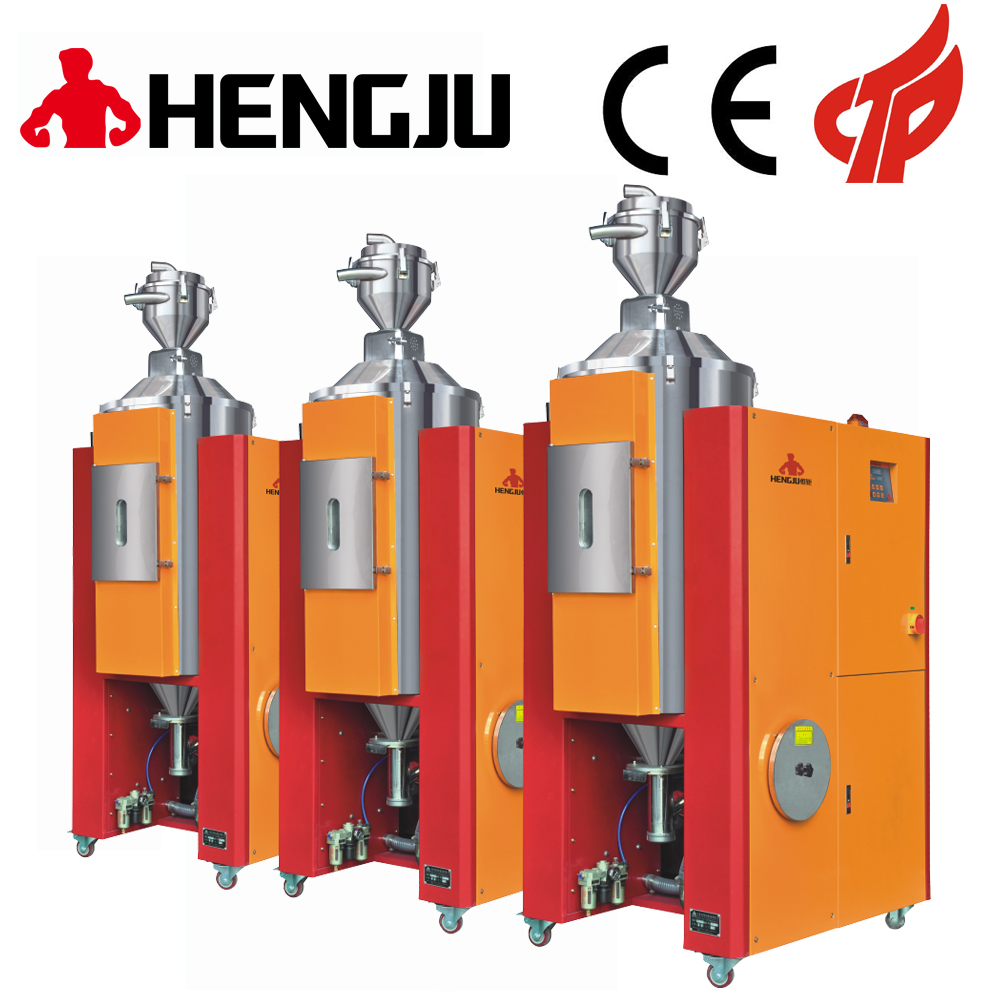
The plastic dryer is throttled by an expansion valve into a low-temperature and low-pressure liquid and enters the evaporator; the low-temperature and low-pressure refrigerant liquid in the evaporator absorbs the heat of compressed air and vaporizes (commonly known as "evaporation"), and the compressed air is cooled A large amount of liquid water is condensed; the refrigerant vapor in the evaporator is sucked away by the compressor, so that the refrigerant passes through the four processes of compression, condensation, throttling, and evaporation in the system, thus completing a cycle.
|